Screen Printing Accessories
Additional Devices for different Applications
Depending on the selected screen printing machine HMI offers different additional devices. With the additional devices, the screen printing machine is adapted to your special printing requirements.
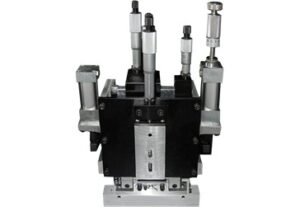
The Mark III Print Head has been improved over its thirty plus year history and continues to be the stock print head on all HMI model precision screen printers.
The heart of the Mark III Print Head is the torsion bar squeegee pressure component of its construction. Similar to the suspension in an automobile, the Mark III head has a torsion bar which is constructed of a material with a consistent spring constant. A linear displacement applied to one end of the torsion bar results in a repeatable pressure at the other end of torsion bar. An even pressure is applied to the print as the torsion bar seeks to correct any change in print pressure resistance or thickness variation.
Manually adjusted controls to set squeegee pressure and down-stop, squeegee level and print dive speed, as well as, flood dive speed and the squeegee angle of attack, on the Mark III make it a hands-on easy to use and easy to understand tool for ensuring proper print performance. All setup controls have incremental readouts and locks to ensure repeatable and secure maintenance of the settings.
Print stroke end points and lift points are set through the printer. The printer also has the ability to assign print and flood strokes to the print head. The squeegee can be used to flood the screen using the appropriate printer cycle. The Mark III has a separate flood dive cylinder that can be set to a different height than the print dive cylinder. This ensures individual control of the squeegee whether it is being used to flood or to print. The Mark III head comes standard with an adjustable metal flood blade, should the process require it.
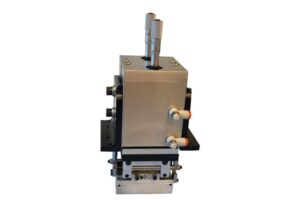
Pneumatic, Programmable Pressure Control with a Computer or Touchscreen Interface.
The print head has two squeegee holders, individually adjusted for angle of attack and for parallelism to the substrate surface. Depending on the setup, each squeegee can be set as either a flood squeegee or a print squeegee. In an alternate print or SMT application, both squeegees can be set as print squeegees. Print stroke end points and lift points are set through the printer.
The DS-IV Print Head is a rugged and reliable dual squeegee head. The addition of digitally controlled pneumatic regulators ensures dependable print results throughout the process run. For assembly methods that require a cost-effective, digitally-assisted dual squeegee head, the DS IV Print Head is the obvious choice.
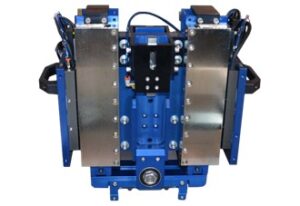
Fully Programmable Servo Pressure, Flood Height, Downstop Location, and Squeegee Leveling to the Substrate.
As a fully automated print head, the SLP-II can be completely integrated into the entire line of HMI automated printers. This allows the operator to create and store several complete printer setup recipes in the printer that can now include print head settings. Additionally, as the process environment changes the SLP-II head will compensate to maintain the preset performance criteria programmed from the recipe.
The SLP-II Print Head has two squeegee holders, individually programmable. Depending on the setup, each squeegee can be setup as either a flood squeegee or a print squeegee. In an alternate print or SMT application, both squeegees can be setup as print squeegees. Each squeegee independently monitors its own performance and adjusts accordingly to maintain consistent print results.
Controls and settings for the SLP-II head are made through the printer. They are user friendly including graphic representations to assist in the association of commands with the performance of the head. Various levels of security can be introduced to minimize variations from a printer setup or to centralize process control.
The SLP-II Print Head is the last piece of the process automation puzzle. In combination with HMI automated features, the printer can now load, align, print and unload without operator interaction. The printer can be used to produce multiple products, requiring multiple setup adjusts, by simply recalling saved setup routines from the printer’s memory. Increased versatility, monitored performance and enhanced throughput on the print line through automation contributes to a higher return on investment.
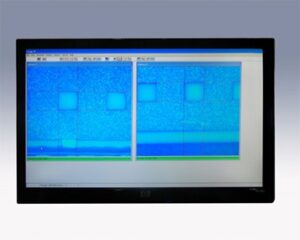
For the customer that requires print-by-print substrate alignment to meet their registration requirements, an economical choice for a fully automated vision system is the HMI Manual Vision Alignment System.
The operator teaches the system to recognize the printed image fiducials. The monitors can then provide a target area, superimposed on the live substrate image. The operator simply adjusts the printer tooling stage until the substrate fiducials align with the targets.
Similar to an automated vision system, the manual system is dependent on fiducial recognition. The fiducial can either be a specific image designed as a fiducial, or the HMI vision system can learn a fiducial from a printed image feature using edge recognition and pixel manipulation.
Fiducial recognition also requires that the video component of the system be able to see the fiducial, regardless of its material composition or size. HMI offers several combinations of lens, lighting and video modules to ensure that the proper magnification, visual spectrum and pixel resolution are available to make the fiducial visible to the processing system and the printer operator.
The HMI manual vision system uses a live printed image for training the system to the screen position. The printed image contains all the additive tolerance errors inherent in screen printing. Screen stretch, image shift, squeegee drag and many other dynamic properties associated with screen printing are all evident in the live printed image.
The training print can be repeated at any time during the life of the screen to take into account the varying registration effects of changing screen conditions, such as tension loss. The ability to adapt to changing screen conditions can help extend the useful life of the screen and reduce overall process costs.
The HMI Manual Vision Alignment System is a cost effective means integrating a precision adjusted registration system into your manufacturing process. The system is easy to use, adaptive to lighting and magnification needs and fiducial elements. In addition, the HMI manual vision alignment system’s image location set point is based on the actual printed image of the screen.
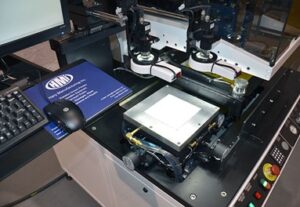
HMI offers an Automatic Vision Alignment System that allows the printer to automatically adjust the screen to substrate registration with each print cycle.
The vision system is integrated with the substrate tooling stage, which becomes motorized to accommodate the incremental adjustment commands sent from the vision system. The vision system is dependent on fiducial recognition. The fiducial can either be a specific image designed as a fiducial, or the HMI vision system can learn a fiducial from a printed image feature using edge recognition and pixel manipulation.
Fiducial recognition also requires that the video component of the system be able to see the fiducial, regardless of its material composition or size. HMI offers several combinations of lens, lighting and video modules to ensure that the proper magnification, visual spectrum and pixel resolution are available to make the fiducial visible to the processing system.
A unique feature to the HMI automatic vision system is the use a live-printed image for training the system to the screen position. Unlike many vision alignment systems on the market today that use static fiducials on the screen, the HMI automatic vision system uses a printed image of the fiducial image. The printed image contains all the additive tolerance errors inherent in screen printing. Screen stretch, image shift, squeegee drag and many other dynamic properties associated with screen printing are all evident in the live printed image.
The training print can be repeated at any time during the life of the screen to take into account the varying registration effects of changing screen conditions, such as tension loss. The ability to adapt to changing screen conditions can help extend the useful life of the screen and reduce overall process costs. Because the HMI vision system uses a live print image, there is no need to require fiducial fill from the screen vendor. Often a source of error due to incomplete filling, irregular fiducial shape or surface projection, screen fiducial fill typically adds cost to the screen.
The HMI Automatic Vision Alignment System is is adaptive to lighting and magnification requirements, it contours to alternate design fiducial elements and its image location set point is based on the actual printed imaged of the screen.
Manufacturer of Screen Printing Accessories: HMI
Your Contact
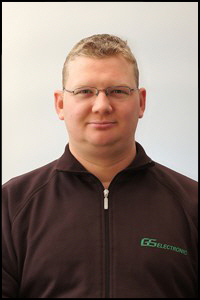
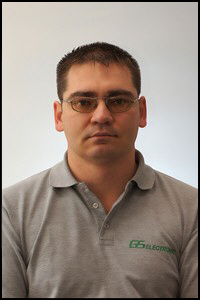